Sustainability at SCHLAADT
All good things come in threes.
Since 2023, sustainability standards have been clearly defined in the EU. In our reporting, we adhere to these highest and most current standards, which also include the CSR reporting obligation in Germany. These cover ecological, social, and financial sustainability.
Economic Sustainability
Product Protection
Production Costs
Transport Costs
Circular Economy
Social Sustainability
Product Protection / Hygiene
Employer Brand:
– Fair Pay
– Career Opportunities
– Respect
– Recognition
Ecological Sustainability
Environmental and Species Protection
Climate Protection
Energy
Conserving Resources
Circular Economy
In summary, we can state that Styrofoam molded parts are convincing in all individual aspects.
Molded parts made of Styropor® are sustainable! In every respect.
EPS IS 100% RECYCLABLE – HOW IS IT RECYCLED?
There are many ways to recycle EPS. And many areas where the resulting materials can be reused. Modern processes lead to the goal. But read for yourself:
USE IN THE POROTON INDUSTRY
In this process, used molded parts are ground. The recovered beads and dust are added to the raw brick material. During the firing process, the Styrofoam particles evaporate. The resulting cavities give the building block its insulation properties.
- Use in construction
- Increased insulation capacity through cavities
THERMAL UTILIZATION
Controlled thermal utilization in a waste incineration plant.
- Replaces oil in district heating power plants
- 1 kg EPS replaces 1.4 liters of oil
- Due to the secondary benefit of thermal utilization, the CO₂ footprint for EPS is significantly reduced, as the CO₂ emissions of the saved oil quantity are deducted from the manufacturing process.
GRINDING AND MIXING
In this process, used EPS molded parts are first pre-crushed and then ground. The recovered beads are de-dusted and rounded. The recycled material produced in this way can be re-mixed in certain proportions for new molded part production, depending on customer requirements.
- Limited mechanical properties
- Bulk density not freely variable
- Limited availability
- Not usable in the food sector
REGRANULATION (MELTING)
In this process, used EPS molded parts are melted using an extruder and processed into PS raw material. This process also offers the possibility of subsequent gassing. This results in EPS (Styrofoam) raw material again, which can be processed conventionally using pre-expanders and molding machines.
- PS/EPS raw material
- Better mechanical properties than ground material
- Freely selectable bulk densities
- Not usable in the food sector
Chemical Recycling – The Recycling Revolution
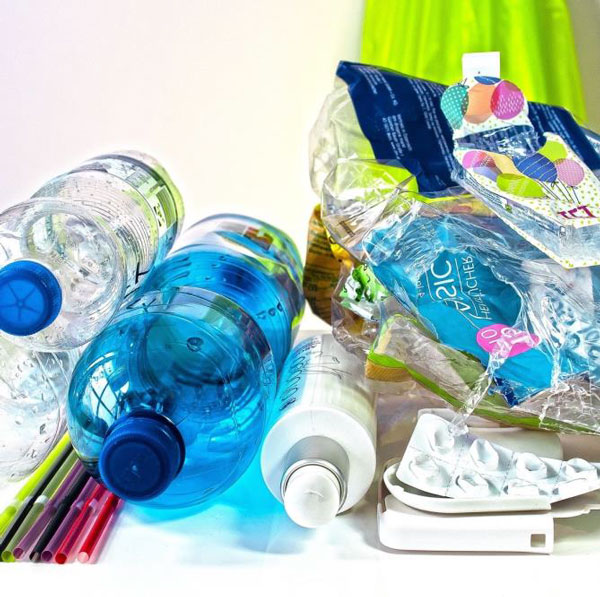
Leading companies in the field of plastics manufacturing have been researching a completely new process for recycling plastics for some time.
The basic idea is to convert the polymer chains of mixed plastic waste back into the starting product, namely monomers (raw gasoline), using a pyrolysis process.
Meanwhile, the first plants are already in operation and the expansion of capacities is in full swing.
- Identical Mechanical Properties
- Freely Selectable Bulk Density
- Even Usable in the Food Sector
NEW! STYROPOR® CCYCLED™
from 100% Mixed Plastic Waste
Biomass Balance Styropor®
- Biomass Balance Styropor® is an EPS based on renewable raw materials.
- At the beginning of the production chain of Biomass Balance Styropor®, renewable alternatives are used instead of fossil raw materials, such as plant waste, vegetable oils or gases.
- The further manufacturing process of Biomass Balance Styropor® is identical to conventional EPS, thus the Biomass Balance Styropor® is indistinguishable in its mechanical and thermal properties.
- Biomass Balance Styropor® has a significantly better environmental footprint, thanks to, for example, much lower CO₂ consumption during production and the avoidance of non-renewable resources.
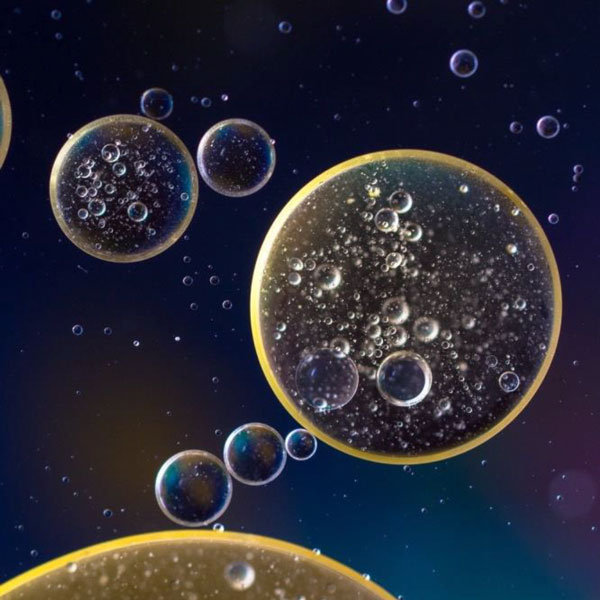